Performance Against Goal
Performance Summary 2024
Recordable Work-related Injuries Rate of Employee
Recordable Work-related Injuries Rate of Contractor
Lost Time Injury Frequency Rate (LTIFR) of Employee
Lost Time Injury Frequency Rate (LTIFR) of Contractor
High-consequence Work-related Injuries Rate(Excluding Fatalities) of Employee
High-consequence Work-related Injuries Rate (Excluding Fatalities) of Contractor
The number of fatalities as a result of work-related injury of Employee
The number of fatalities as a result of work-related injury of Contractor
Management Approach
Structure of the Occupational Safety, Health and Environment Committee
The Company strictly adheres to the law by appointing 1) an area-level Committee of Occupational Safety, Health and Working Environment that focuses on employee participation by electing representatives from employers and employees on a proportionate basis as required by law, and hosting monthly meetings. Beyond stipulation by the law, the Company has implemented Occupational Safety, Health and Environmental Management across all operational areas of the Company. Secondly, the Company has appointed 2) a function-level Sub Committee of Occupational Safety, Health and Working Environment that is elected every 2 years and has the responsibility of assessing issues from the area-level Committee of Occupational Safety, Health and Working Environment and budget approvals. Thirdly, the function-level Sub Committee of Occupational Safety, Health and Working Environment is under the supervision of 3) the Occupational Safety, Health and Environment Committee that is responsible for relaying the policy to each operation function and aligning the same standard with employees at every level within the organization, including contractors and suppliers across the Company’s supply chain.
Furthermore, the Company uses the evaluation of the risks toward Safety, Occupational Health and Working Environment to improve operation processes, work areas, and employee training as well as equipment in 7-Eleven stores.
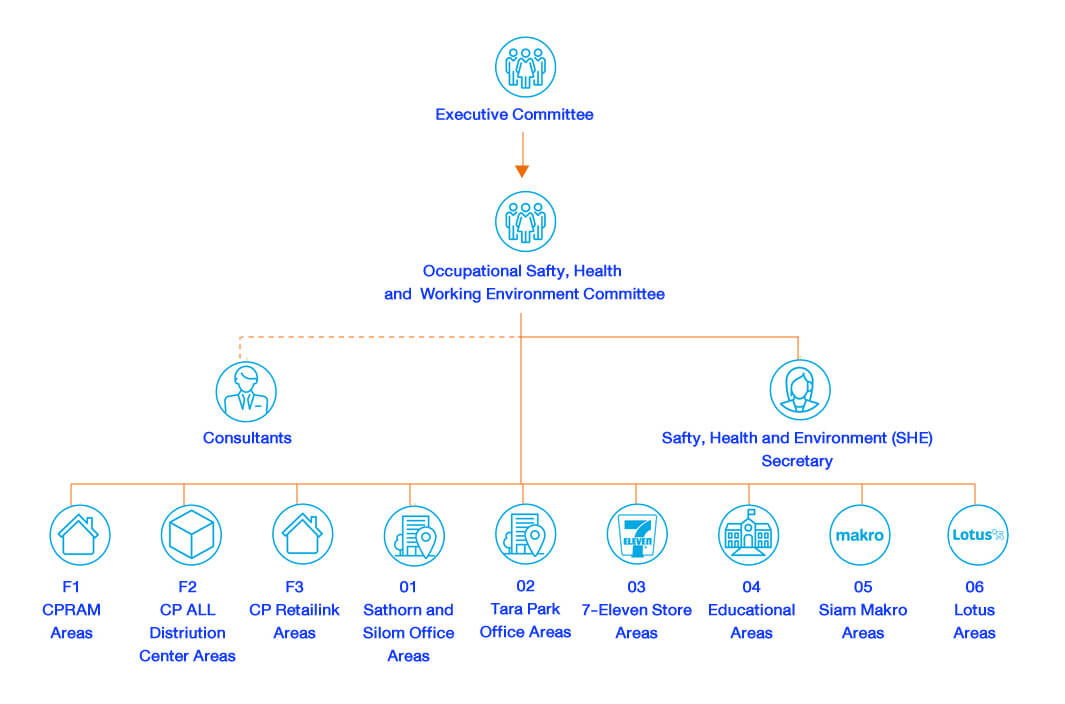
Elevate the Level of Occupational Health, Create a Safe Workplace
The Company prioritizes respecting occupational health, safety, and environmental aspects in the workplace, and safety during employees’ work time, including contractors who come to work in the company’s area. by establishing policies on safety, occupational health, and the environment in workplace, including managing and ensuring safe working conditions according to international standards to the law and aims to become an accident-free organization by 2030. Additionally, the Company has set up a committee for safety, occupational health, and workplace environment policies within the marketing and distribution business group. The Company set policies, operational guidelines, and plans to develop occupational health and safety systems, a committee has been established to evaluate the effectiveness of safety, occupational health, and environmental management, in collaboration with the Charoen Pokphand Group, to establish a committee for preventing severe accidents and minimizing potential impacts. Other activities include organizing a workshop seminar for the Occupational Safety, Health, and Environment Committee annually, as well as raising the level of management to the international level. The objective is to create a positive impact on the environment both inside and outside the organization. The Company ensures that employees work in safe working conditions.
OHS risk and hazard assessments to identify what could cause harm in the workplace
Risk Assessment Process
The Occupational Safety, Health and Environment Committee assigned executives at a department level or equivalent in each area to assess the risks to identify activities/area/work characteristics, such as driving a motor vehicle/motorcycle, chemicals, light, sound, by considering the work involved. Work from offsite areas that are at risk, including work related to contractors and including a review of risks in case of changes in control of raw materials / activities / processes / new products / flowcharts of workflow. There is also the case of new laws / complaints / accidents and risk reduction considerations once a year by assessing risks in both routine and normal situations; and irregular working situations that occur from time to time, along with assessing the risk of behavior affecting work activities, as well as identifying hazards and assessing the significance of the nature of safety problems under the 7 categories, consisting of 1) Environment 2) Machinery, tools, equipment 3) Materials / raw materials 4) Actions or behaviors (human behavior) 5) working conditions 6) Employees 7) Social Factors.
Then the organization jointly assesses the risks by using the criteria of 1) assessing the likelihood of loss from hazard 2) assessing the severity of the loss from hazard, and registering a risk to further prioritize and determine risk control measures.
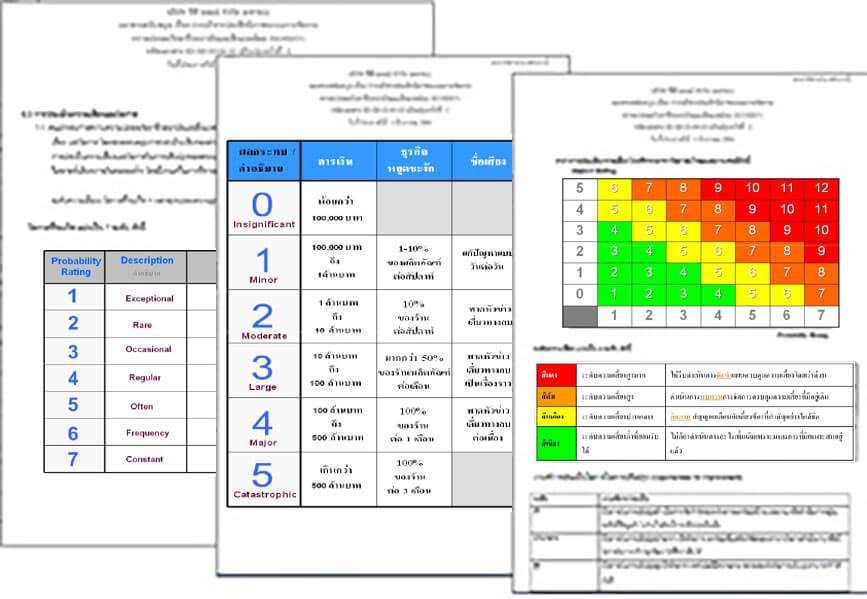
Prioritization and integration of action plans with quantified targets to address those risks
Those who are responsible for each area must prioritize risks to determine risk management measures and propose for approval from the Occupational Safety, Health and Environment Committee.
Risk Level | Detailed Operations |
---|---|
Unacceptable (5) | Stop the operation immediately and find solution to decrease the risk level to an acceptable level. There must an investigation into the causes and apply the solution before a permission to resume the operation is granted. There must also be controlling measures, and there must be evidence ready for investigation throughout an allotted time |
High (4) | Decrease the risk level to an acceptable level by revising the existing controlling measure / canceling / set a new measure / set objectives, goals, and projects, as well as there must be evidence ready for investigation throughout an allotted time |
Medium and Acceptable (2,3) | Reviewing the appropriateness of existing controlling measure to continuously control risk to stay at an acceptable level and a line manager must review the operation thoroughly |
Small (1) | A line manager must review the operation constantly |
In addition, they must assign it to relevant people to prepare a project action plan and to set project objectives, quantitative goals and responsible persons, and propose the Safety, Occupational Health and Work Environment Committee for consideration and approval of projects and plans. Read more about the project at —> Sustainability Report 2024 (Page. 197-203)
Project example, objectives, and goals
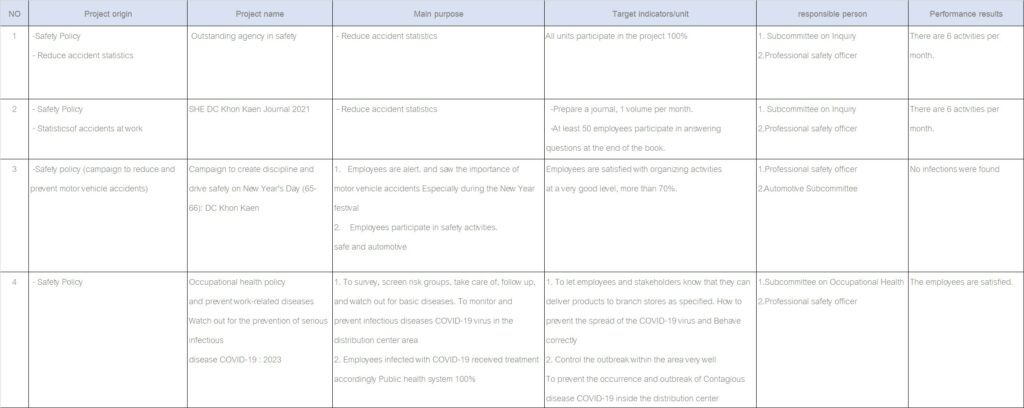
Project example, objectives, and goals
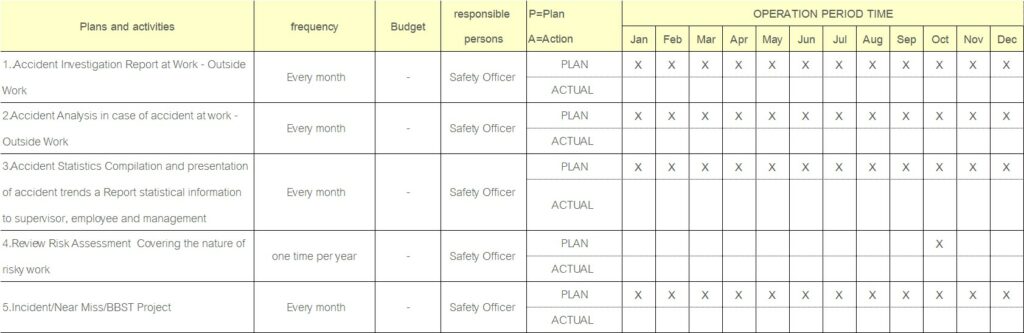
The Company prioritizes respecting the rights of occupational health, safety, and the working environment of employees and contractors working in the Company’s areas. This includes establishing safety and occupational health policies, as well as ensuring that work areas meet international safety standards and comply strictly with relevant laws. The goal is to create an accident-free organization by 2030.
The Company has established a committee to review and evaluate safety, occupational health, and environmental management. This committee is responsible for setting policies, operational guidelines, and developing occupational health and safety systems. Additionally, it works with Charoen Pokphand Group to assess the effectiveness of management practices to prevent serious accidents and minimize potential impacts. The Company also organizes annual workshops on safety, occupational health, and the working environment (OSH) to align management with international standards and reduce environmental impacts both inside and outside the organization, ensuring that all employees work in a safe environment.
Additionally, the Company provides opportunities for employees to report accidents and high-risk activities, and has established procedures for investigating accidents. An accident investigation committee is responsible for investigating and analyzing the incidents and developing appropriate corrective actions. From the safety risk assessment in 2024, it was found that there are two high-risk activities: 1) Rider Delivery and 2) Work involving transportation contractors.
In 2024, there was a fatal accident from high-risk activities. The report summarizes the cause and preventive measures as follows:
High-risk activities |
Rider Delivery |
Unsafe Situation (cause) |
|
Unsafe Actions (cause) |
|
Solution/Preventive Measures |
|
Occupational Health and Safety System Development Plan for 2024
The Company enhances occupational health and safety management in the workplace for employees and stakeholders by obtaining ISO 45001:2018 certification. This involves organizing training and appointing certified experts from the distribution centers to develop the system in collaboration with target areas. The Company has also developed guidelines to assess and select locations that are ready to apply for certification, undergo evaluation by external auditors (Third Party), and prepare for the actual audit, including conducting annual surveillance audits to maintain system standards.
Occupational Health and Safety (OHS) to the international standard ISO 45OO1: 2O18
2019 – 2021 (Phase 1) | 2022 (Phase 2) | 2023 | 2024 | 2025 | |
---|---|---|---|---|---|
|
|
|
|
|
|
|
Assess and monitor by Independent external verification of health, safety and well-being
In 2024, the Company received ISO 45001:2018 certification for an additional 5 locations: CDC Phuket distribution center, BDC Mahachai distribution center, BDC Chonburi distribution center, BDC Hat Yai distribution center, and BDC Khon Kaen distribution center. This brings the total target areas certified to 90% of the 30 target distribution centers, with plans to expand in 2025 to an additional location, the ALL COMPLEX distribution center.
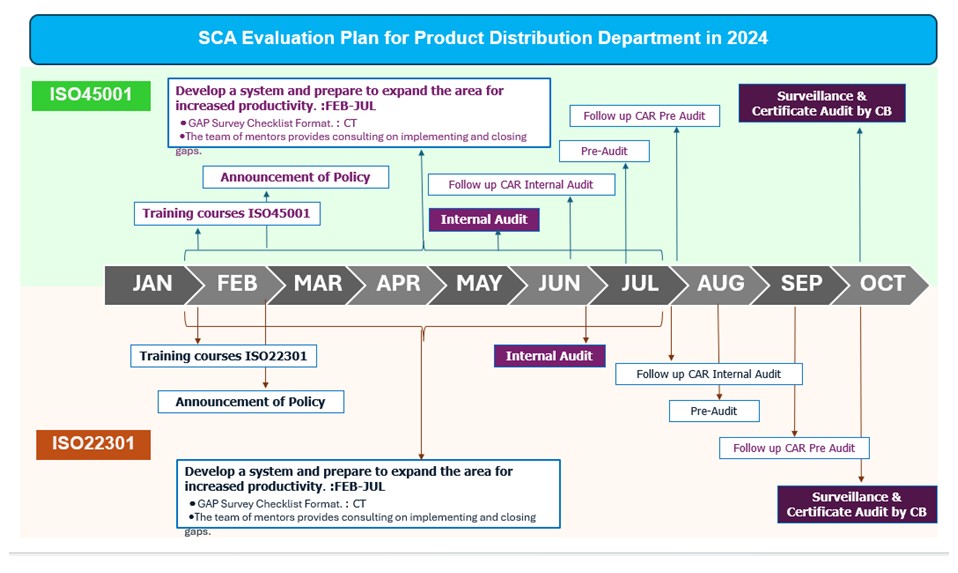
- CP ALL ISO 45001 Certificate for Hat Yai (CDC&BCD)
- CP ALL ISO 45001 Certificate for Chonburi (RDC&BCD)
- CP ALL ISO 45001 Certificate for Nakhon Sawan (RDC&BCD)
Policy, Goal, and Safety and Risk Assessment
The Company establishes policies for safety, occupational health, and environmental conditions in the workplace, along with setting targets towards conducting business with reduced numbers and rates of work-related fatalities and injuries of employees and all subcontractors. The Lost Time Injury Rate (LTIFR) is aimed to decrease by 40% and reach zero by the year 2030. The Company has conducted a risk assessment in 4 main steps by identifying areas that may cause hazards in the workplace, namely 1) Identify activities, areas, and nature of work, 2) Identify hazards, 3) Assess risks and 4) Prepare a risk registry. This includes prioritizing and integrating action plans with quantitative goals to determine risk management measures. The information was ready to be submitted to the Committee on Safety, Occupational Health, and Environment to consider and approve the project and implementation of monthly and annual plans. The Company also facilitates a channel of communication for employees to report accidents that occurred or have high risks of occurring. The objective is to reduce, control, and prevent any accidents that may occur.
Integration of actions to prepare for and respond to emergency situations
The Company has integrated operations to prepare and respond to emergency situations.
An Example of the Operation
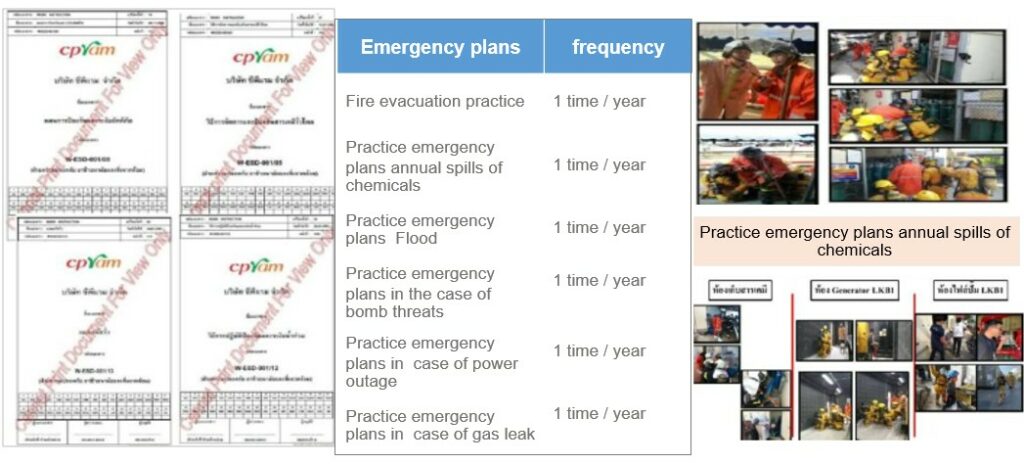
An Example of an Annual Emergency Plan Practice Schedule
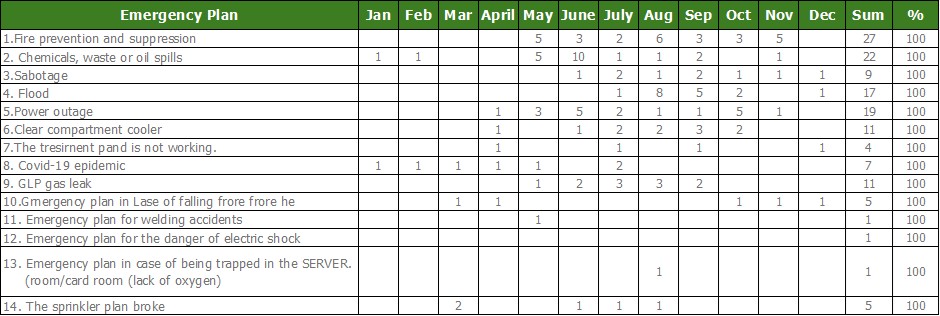
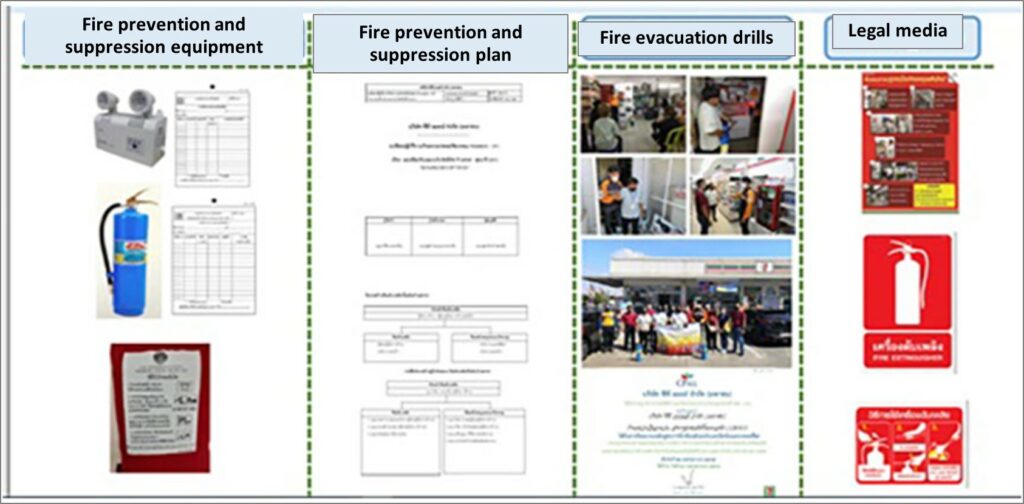
Evaluation of progress in reducing/preventing health issues/risks against targets
Occupational Safety, Health and Environment Committee evaluates and monitors the progress of projects and plans every month, both qualitatively, quantitatively, and proactively. Examples are checking the working environment, safety inspection according to the inspection plan of machinery, equipment, maintenance of machinery, equipment, health checks, and along with the objective review and goals of the project once a year.
Examples of Quantitative Tracking to Measure Progress of Objectives and Goals for 2024
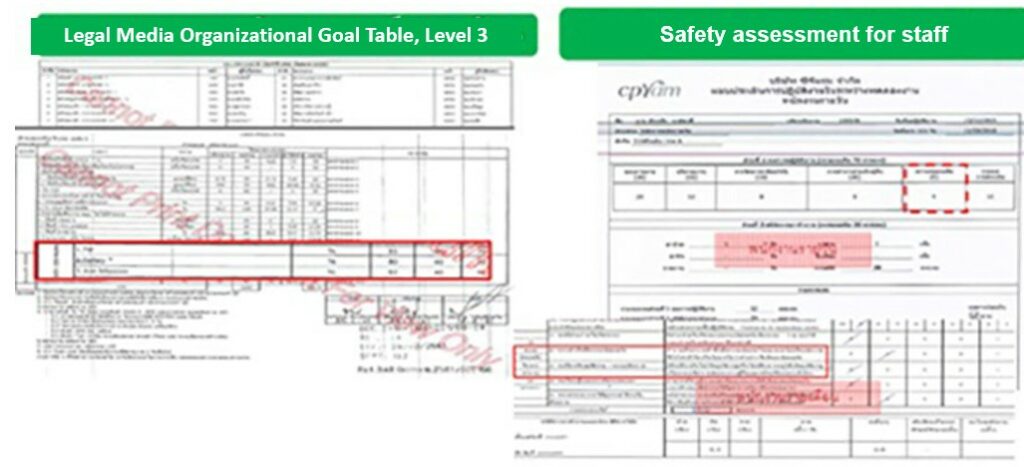
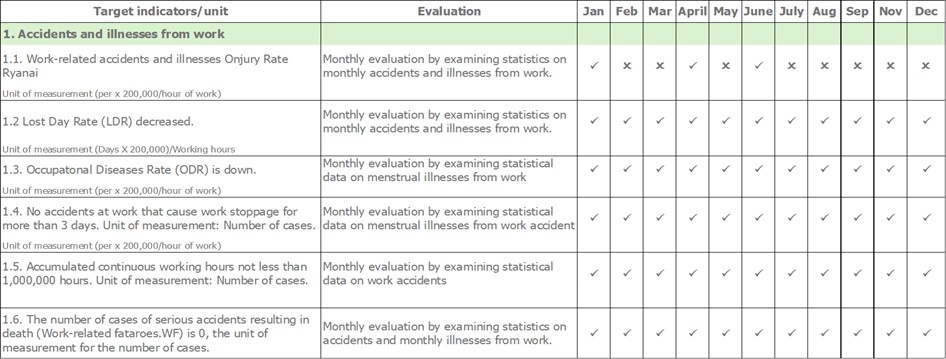
An example of the proactive monitoring of the safety of the 7-Eleven store’s operating line by the Quality Store Standard Inspector once a month
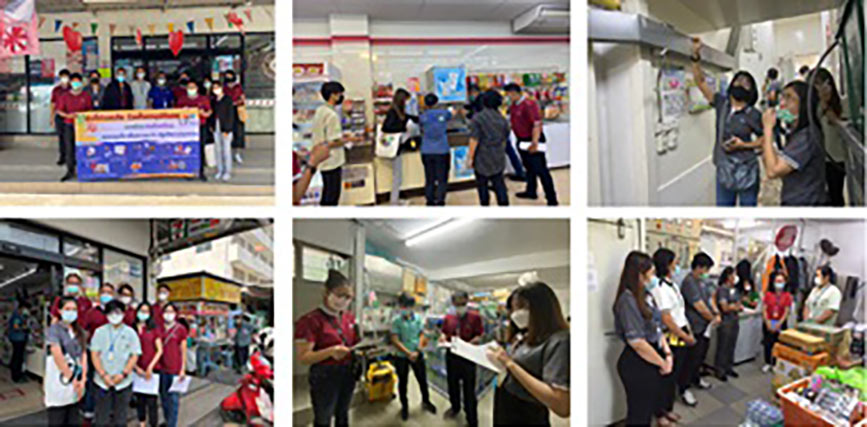
An example of proactive health checks based on risk factors
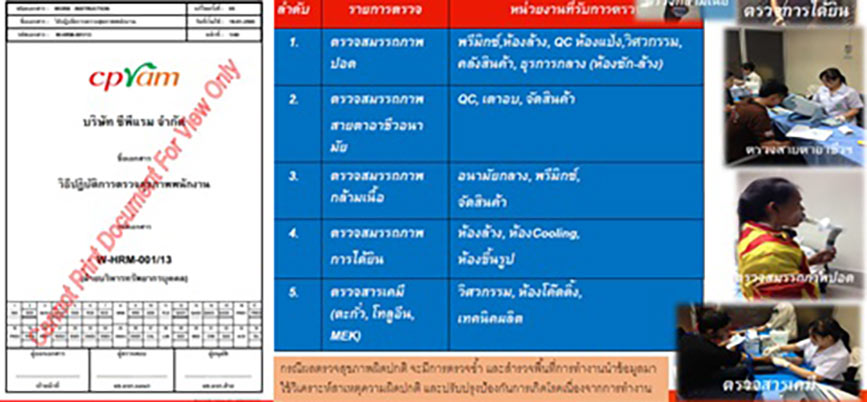
Internal inspections
The Company has established a systematic internal audit process to ensure that the occupational health management system and organizational safety has been implemented continuously and effectively. This is accomplished by collaborating with Charoen Pokphand Group to establish a Safety, Health and Environmental management effectiveness assessment program (SHE) to prevent serious accidents and reduce their impact. This is carried out by the central committee once a year under the criteria for evaluating the effectiveness of SHE as follows.
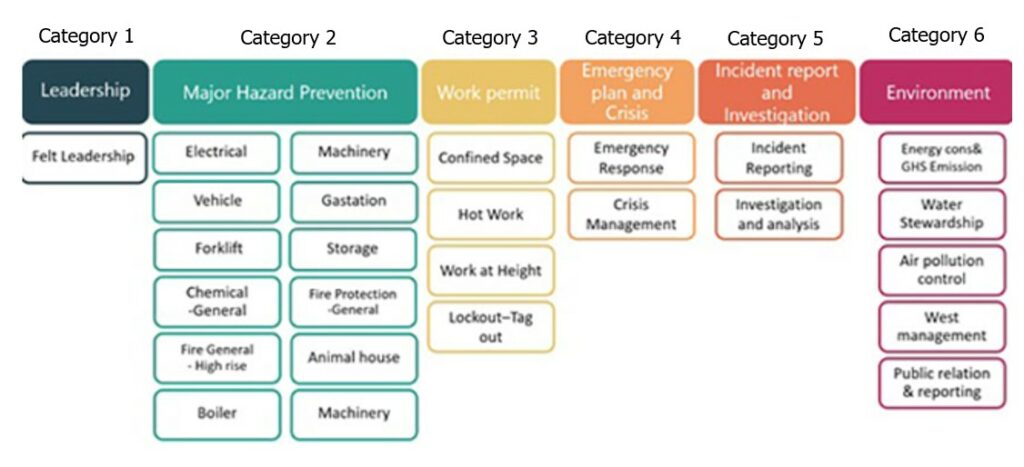
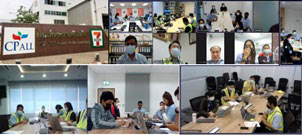

The Company has an integrated workflow to prepare for and respond to emergency situations, as well as operated with works related to safety, occupational health, and environmental conditions in the workplace, while also promoting a good quality of life for employees within the organization through three main programs, as follows:
1. Decent Quality of Life for Employees and Family Program
Flexible Work Arrangement
The Company promotes work-life balance by allowing employees with permanent employment status to choose the following work schedules that are aligned with their lifestyle. The specified periods are as follows:

flexible working
hours
07.30-17.00
08.00-17.30
08.30-18.00
09.00-18.30
09.30-19.00
The Company also has a policy and guidelines allowing employers to choose their work location (“Work Anywhere”), in addition to being able to work from home for a maximum of 3 days each week as well as supporting a work system that supports work Option to work at any location So that employees can communicate and access systems to work efficiently, such as online meeting systems. Communication system via CP ALL Connect and True Virtual Connect, etc.
Employee Family Welfare Project
The Company prioritizes the well-being of both employees and their families to foster strong relationships and a sense of security within the family. This approach helps reduce employee concerns and strengthens their engagement with the organization. The Company is committed to supporting employee family welfare for a better quality of life through the following benefits:
Learning activities for employees’ children |
To ease the burden on parents and provide children with valuable learning experiences and productive use of their free time, such as:
|
Analysis services for the capability and personality of children and youth in the Luk Riang Scholarship Program |
|
Breastfeeding support in the workplace program
The Company provides benefits for female employees to support them in their journey to motherhood, from pregnancy and childbirth to raising their children, as follows:
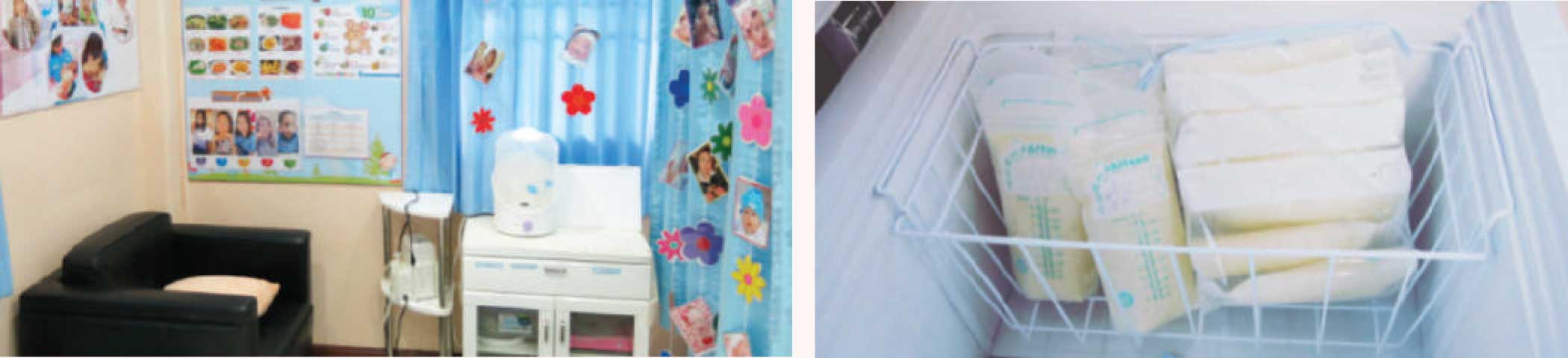
Impacts and Benefits

Reduce the resignation rate of female employees after childbirth

Foster positive relationships between employers and employees
Health for ALL
The Company prioritizes and respects employees’ health rights by encouraging participation in activities and exercise programs to promote well-being and reduce the risk of diseases such as obesity and diabetes. Currently, 17,474 employees have joined the program.
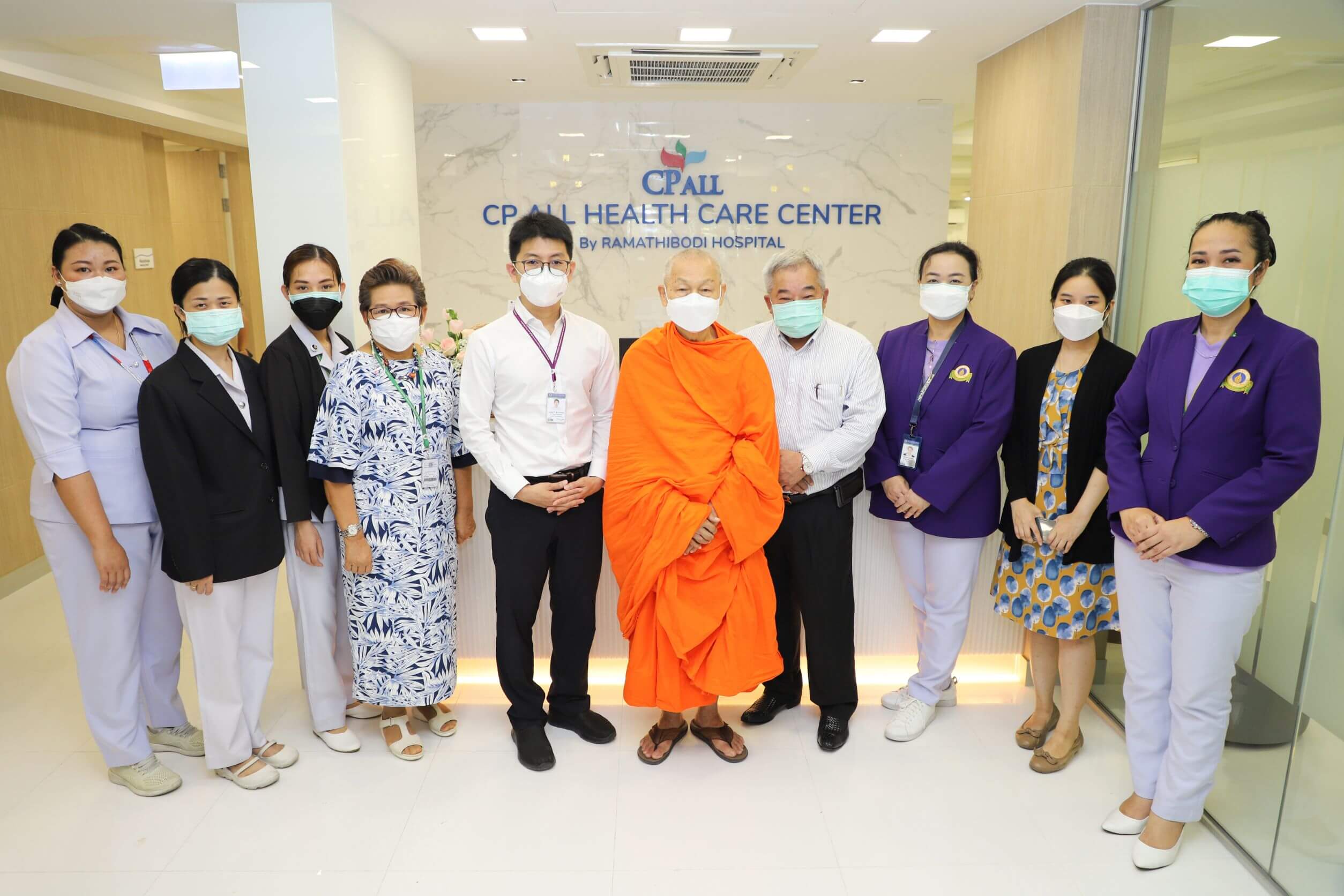
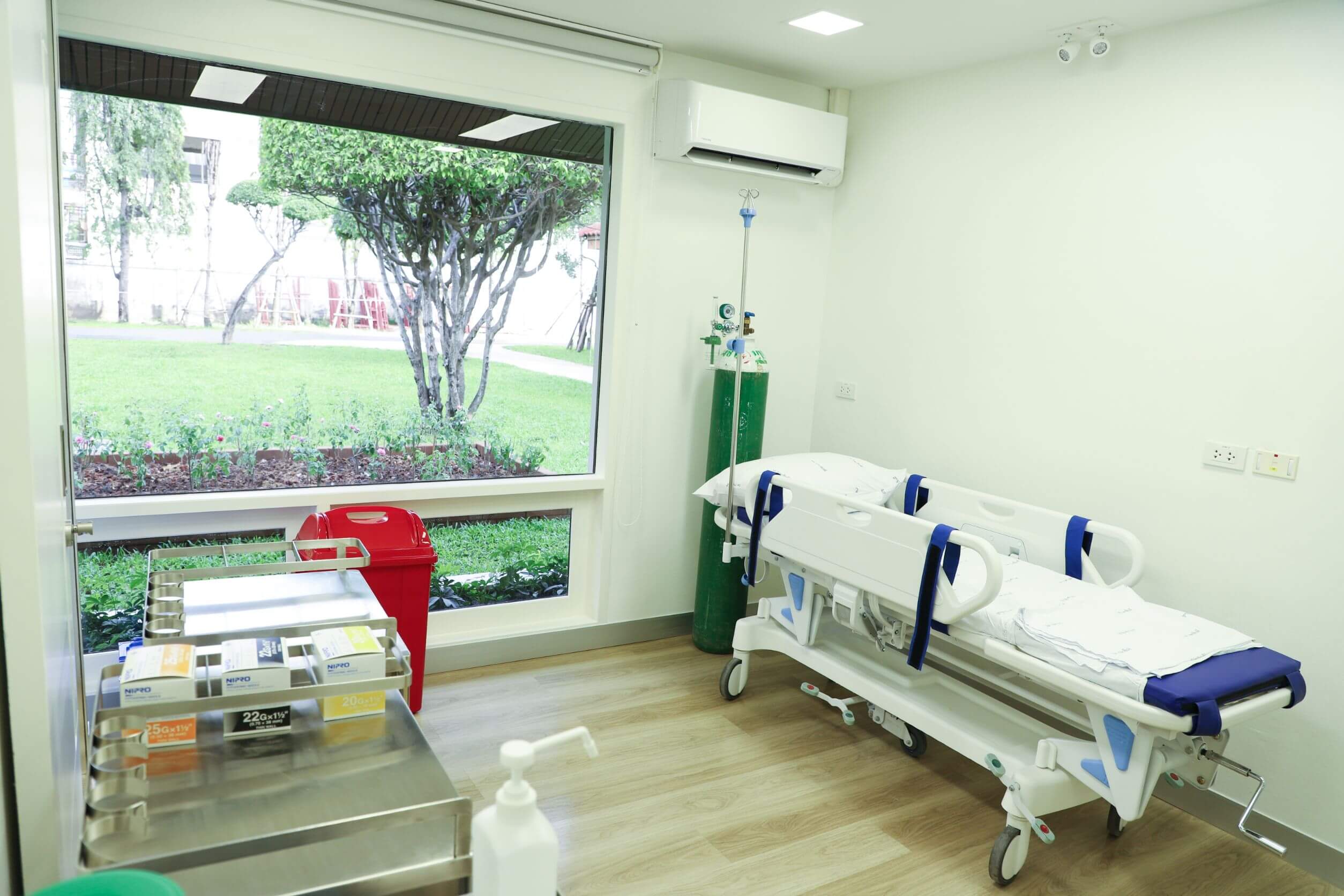
2. Safety Risks Reduction Program
Safe Driving for Delivery Employees (Rider)
The Company has established strict measures for delivery employees to comply with legal requirements, such as wearing helmets, possessing a valid driver’s license, having compulsory motor insurance (Por Ror Bor), and voluntary insurance as well as completing safe driving training. The Company regularly reviews and communicates safety guidelines for driving while on duty as follows:
1. Improve safety measures for vehicle usage |
|
2.Foster a culture of safe driving |
|
3. Provide accident prevention equipment |
|
4. Strengthen supervision and monitoring measures for delivery employees (Rider) |
|
5. Pilot the use of electric motorcycles |
|
The Company regularly monitors accident reports. In 2024, it collaborated with the Honda Riding Training Center, Yamaha Riding Center, driving schools, and mobile training units to provide safety training for employees. The training sessions, conducted by expert instructors, include both theoretical and practical components in standardized training facilities. The Company aims to ensure that all employees nationwide receive standardized training to achieve zero accident rates.
Additionally, the Company has developed the Last Mile application to track the work of Rider employees. This initiative aims to enhance operational safety, maintain high standards, and improve efficiency in monitoring work performance.
Freight Transport Safety Management Program
CP ALL aims to reduce the risk of workplace accidents for transportation contractors through a freight transport safety management program. This project aims to: 1) Establish safety standards for freight transportation. 2) Consistently communicate to raise awareness of safety among managers, staff, delivery unit personnel, freight transportation operators, and freight transport employees. The Company also promotes safe driving practices and prevention of potential accidents involving freight vehicles. 3) Reduce losses from freight transport accidents, both in terms of life and property, by reducing the number of freight transport accidents and minimizing delays in product delivery caused by such accidents. 4) Align with the sustainable development goals of the CP Group’s “Zero Accident” strategy. This initiative targets all distribution centers nationwide by 2030, as follows:
TRAIN-THE-TRAINER
CP ALL has developed safety standards training for transportation employees using the TRAIN-THE-TRAINER approach. This aims to educate transportation contractors about safe driving practices and conduct inspections on freight vehicles and analyzes accidents that occur at distribution centers to identify preventive measures and solutions.
DRIVING CONTEST
The contest is a competition for safe and efficient driving among transportation employees, using GPS tracking and recording data of freight vehicles. The objectives are: 1) To encourage consistently safe and efficient driving behavior among transportation employees. 2) To utilize existing GPS technology for tracking freight vehicles effectively. 3) To reduce accidents and losses resulting from transportation accidents. Additionally, rewards are given to transportation employees with good driving behavior.
DRIVING BEHAVIOR MONITORING
Elevating the tracking of driving behaviors of transportation employees with GPS systems involves monitoring their driving behaviors using GPS technology. There is an automatic warning system in place to notify when speeding occurs beyond the standards. The receipt of warnings will affect procurement evaluations upon contract expiration and wage rate adjustments because risky behaviors increase the likelihood of accidents and result in losses for the Company.
The operation includes establishing rest stops for long-haul transportation contractors on routes exceeding 250 kilometers or taking more than 4 consecutive hours to travel. These stops must provide safe parking areas for contractors to rest and reduce fatigue from driving.
Security officer training program
CP ALL requires security companies under contract to provide training on the knowledge necessary to perform their duties, such as policies and procedures related to human rights. These include security as everyone’s basic right, no violence against others, even if they are the perpetrators, security officers do not have the right to arrest anyone unless they are caught in the act of crime, and the accused has the right to be presumed innocent until proven guilty. All security officers must be fully aware of this guideline prior to working. In 2024, there were no human rights complaints against company security personnel. And 100% of outsourced contract security personnel are trained.
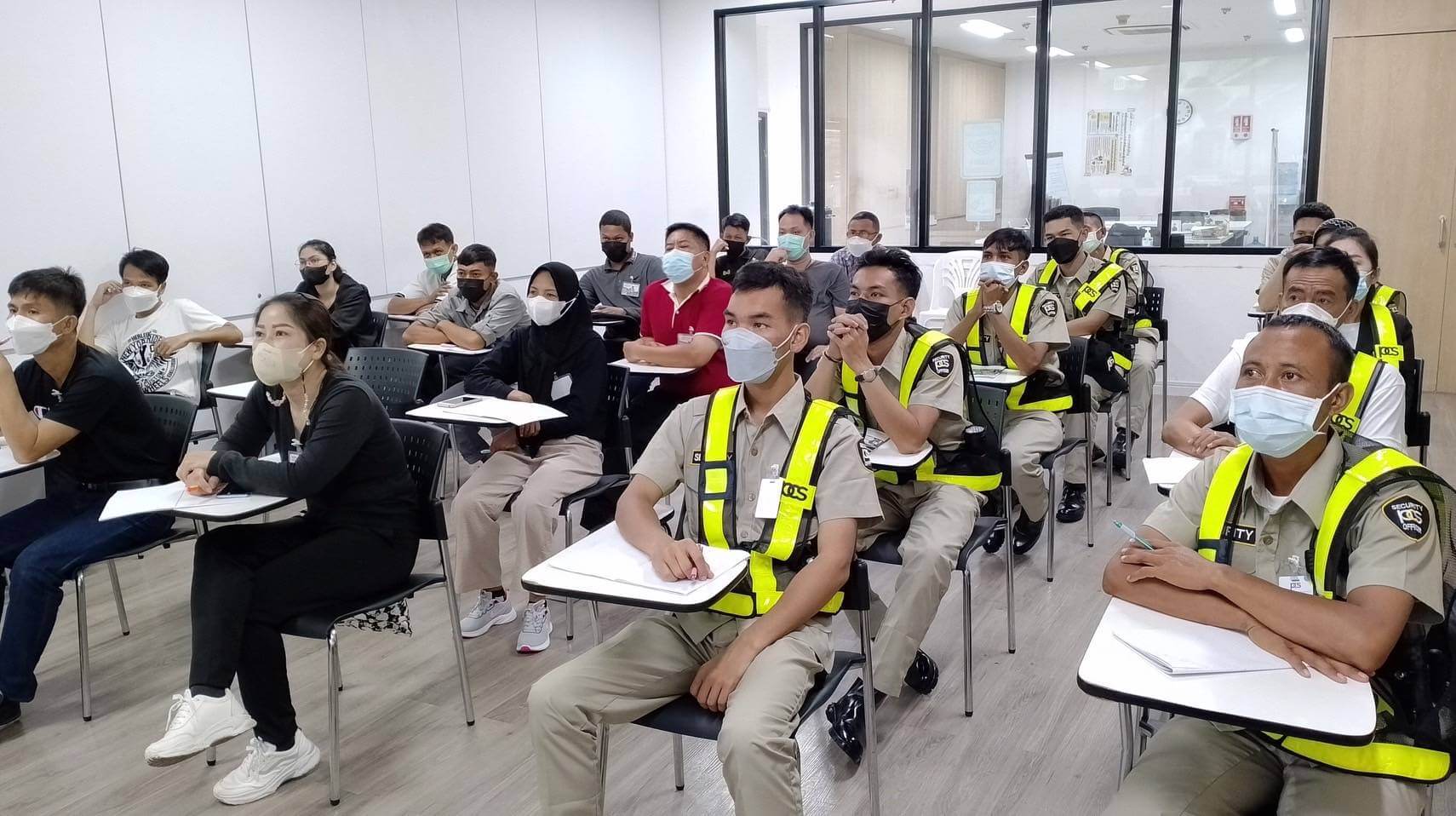
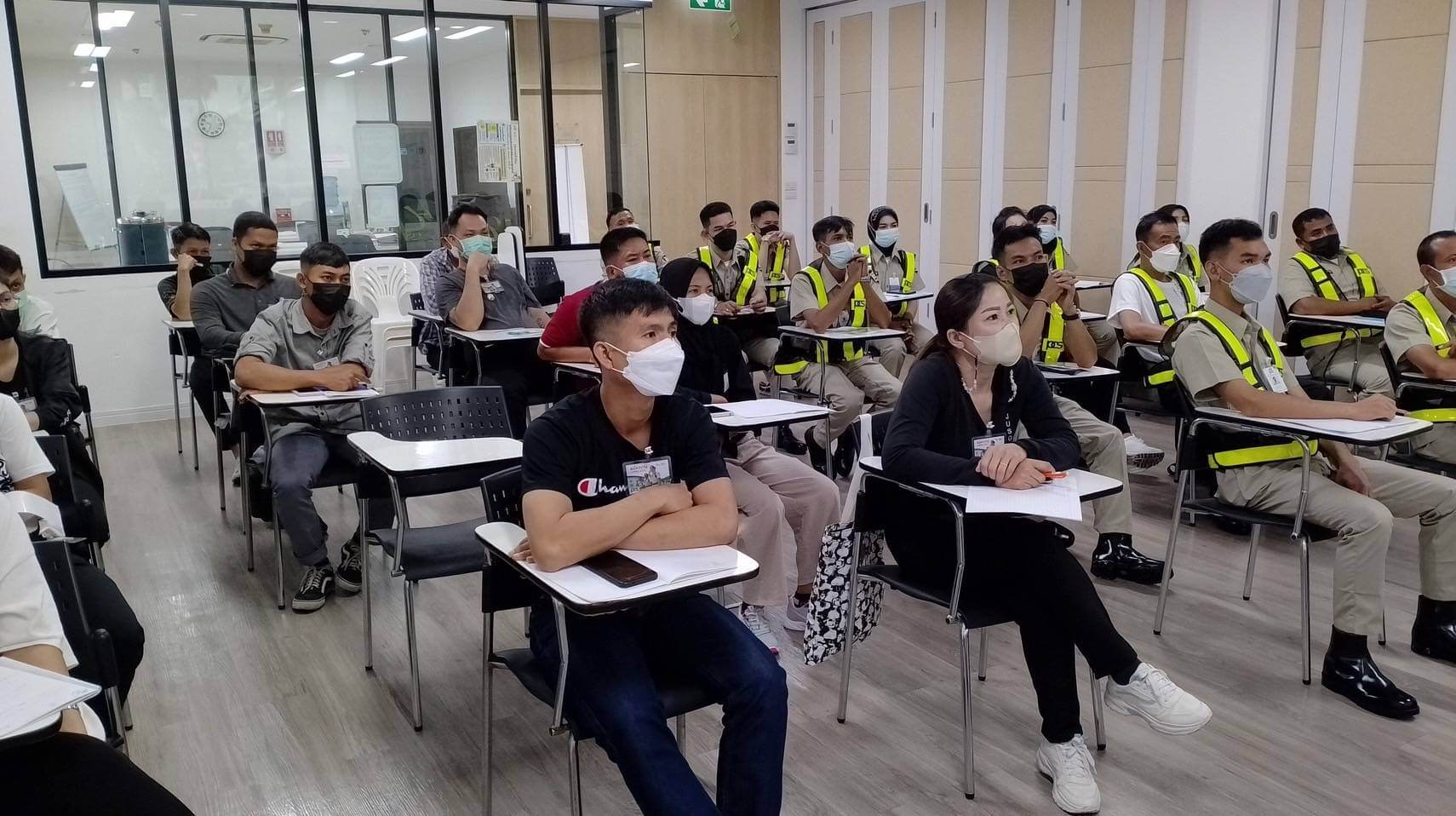
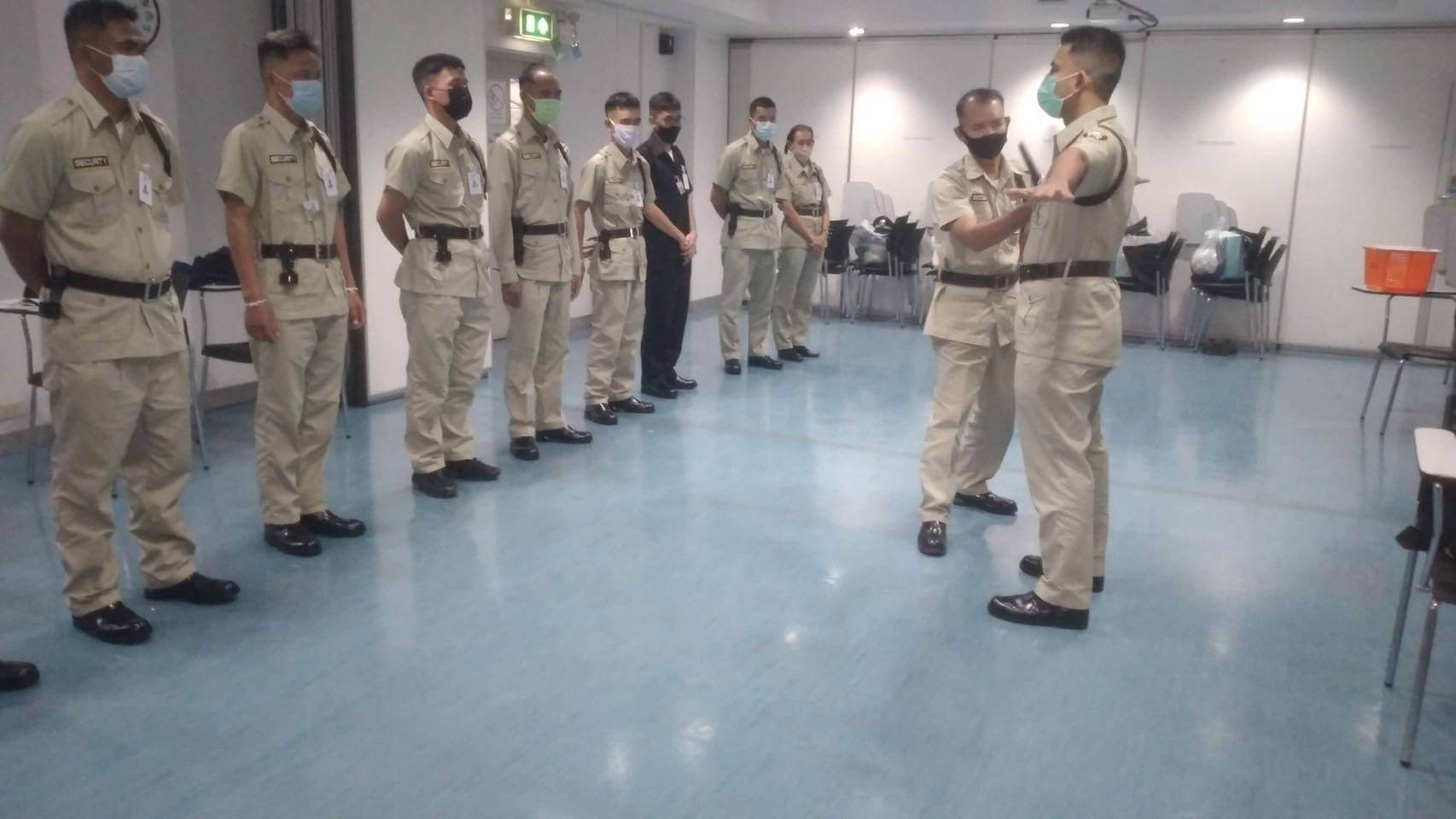
Impacts and Benefits

Outsourced contract security staff are trained
Safety Innovation Project
CPRAM Co., Ltd. (Lat Krabang) has improved the product forming process under the “Efficiency Enhancement of Croissant Forming Process for Easier, More Comfortable, and Safer Work” project. The initiative focuses on making work easier, more comfortable, and safer by implementing semi-automatic safety innovation technology in the sheet-cutting and rolling stages, replacing manual labor. This reduces risks associated with blade contact, exerting pressure on blades, and blade cleaning.process under the “Efficiency Enhancement of Croissant Forming Process for Easier, More Comfortable, and Safer Work” project. The initiative focuses on making work easier, more comfortable, and safer by implementing semi-automatic safety innovation technology in the sheet-cutting and rolling stages, replacing manual labor. This reduces risks associated with blade contact, exerting pressure on blades, and blade cleaning.
Additionally, the upgrade has increased croissant production capacity. As a result, in 2024, the number of accidents involving cuts and fatigue from manual slicing was reduced to zero.
3. Ergonomic Risks Reduction and Stress Management Program
CP ALL Health Care Center
The Company operates a health care center project for the continuous care of employees’ health, through the cooperation of medical personnel, including a team of doctors, nurses, and physiotherapists from Ramathibodi Hospital. There are 5 main areas of care, as follows: 1) General medical examinations 2) Specific diseases such as bone diseases, skin diseases, eye-ear-throat-nose diseases, etc. 3) Physical therapy (at the doctor’s discretion), 4) Patient beds for recovery, and 5) Providing assistance in case of emergency illness or crisis. There are also other welfare benefits, such as prescriptions for employees with prescriptions or medical certificates without having to pay in advance, and employees can choose to receive medicines from home or the office. The Company promotes access to vaccines according to employees’ rights for employees at all levels and provides employees with additional vaccines for various diseases. The Company also provides rehabilitation services for patients with aches and pains, stiff muscles, weak legs, back pain, or suffered from office syndrome, along with providing consulting services and health care by expert physiotherapists. In 2024, there were 1,878 employees and executives participating in the project.
Ongoing Project: Stretching to Reduce Illness – Year 5
The Company implemented the “Stretching to Reduce Illness”program in an online format, inviting specialists to provide knowledge on office syndrome, physical therapy, and traditional Thai medicine. Experts from eXta Health & Wellness educated employees on proper posture and ergonomics to prevent muscle pain. In 2024, a total of 251 employees.
Ongoing Project: Promoting Workplace Wellness: “Health Massage Activity” – Year 2
The “Workplace Wellness Promotion Project: Health Massage Activity” was organized to help employees relax their muscles, reduce office syndrome issues, and improve their overall health. The primary target group consists of employees experiencing muscle pain and those at risk of office syndrome. A total of 884 employees participated in the program. Additionally, CPRAM Co., Ltd. (Khon Kaen), in collaboration with the Traditional Thai Medicine Department of Sirindhorn Hospital, provided health massage services, chiropractic adjustments, and health consultations twice a month. As a result, 99.07% of participants reported improvement in their muscle pain.
Procedures to investigate work-related injuries, ill health, diseases and incidents
The investigation for work-related injuries
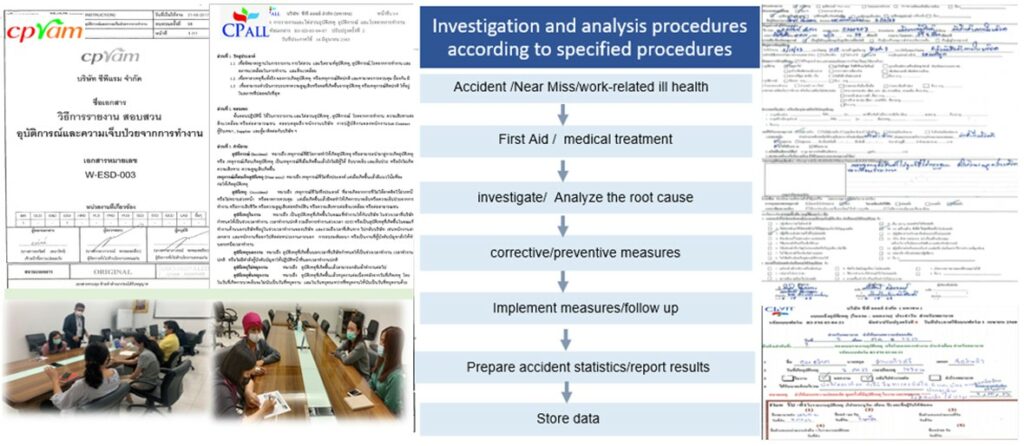
Work-related Injury Examination for the Rider Group
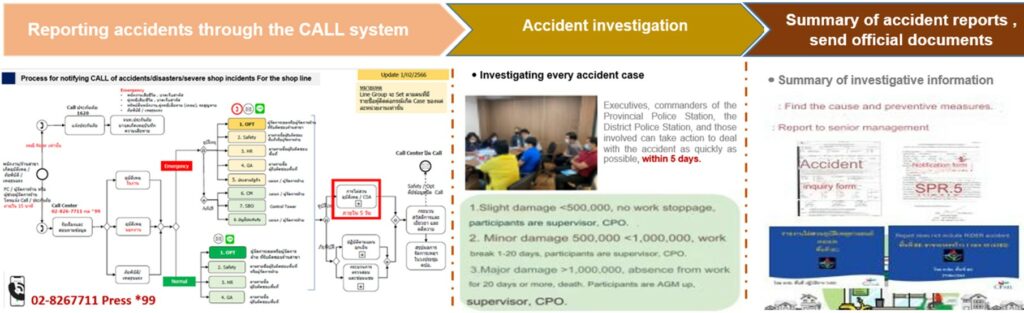
OHS training provided to employees and/or other relevant parties to raise awareness and reduce operational health & safety incidents
The Company gives great importance to knowledge development, employees’ performance, and raising awareness and communicating necessary information to stakeholders, including analyzing the need for training and conducting training, as well as offering knowledge sharing sessions and courses relevant to tasks at hands for employees to be able to perform tasks well and safe in risky operations. Examples of various relevant projects are as follows:
Safety Committee Workshop Project. The goal is the path to zero accidents
Safety and Environmental Management System Training Program for Personnel Development
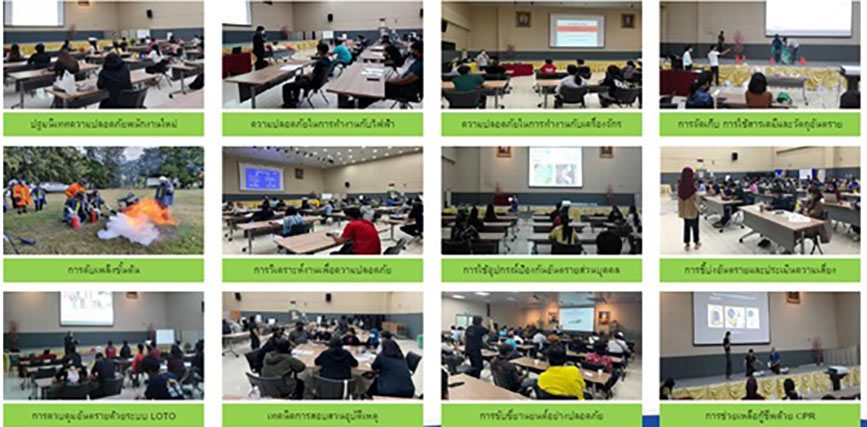
Training program to increase safe driving skills for 7-Eleven store staff
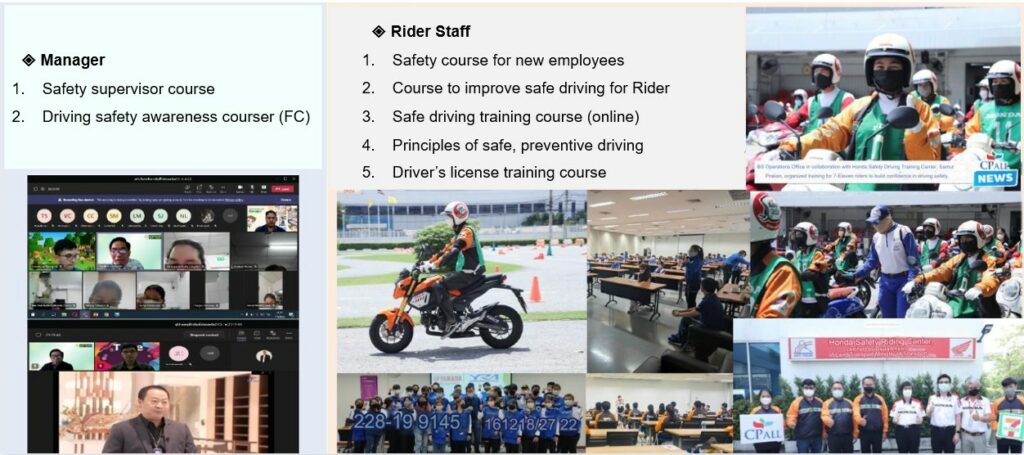
The program in raising awareness, changing safety behaviors for distribution center employees and transport contractors
(Kiken Yochi Training : KYT)
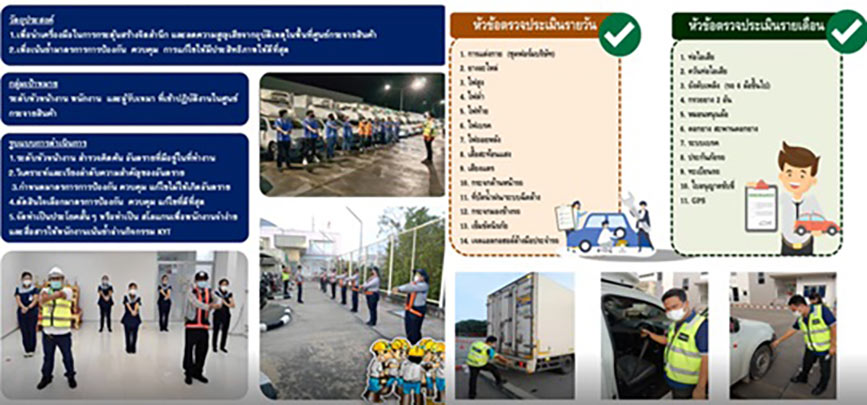
Training program for driving license test for PT vehicles and forklift vehicles, the coursework involves theory and practice for drivers
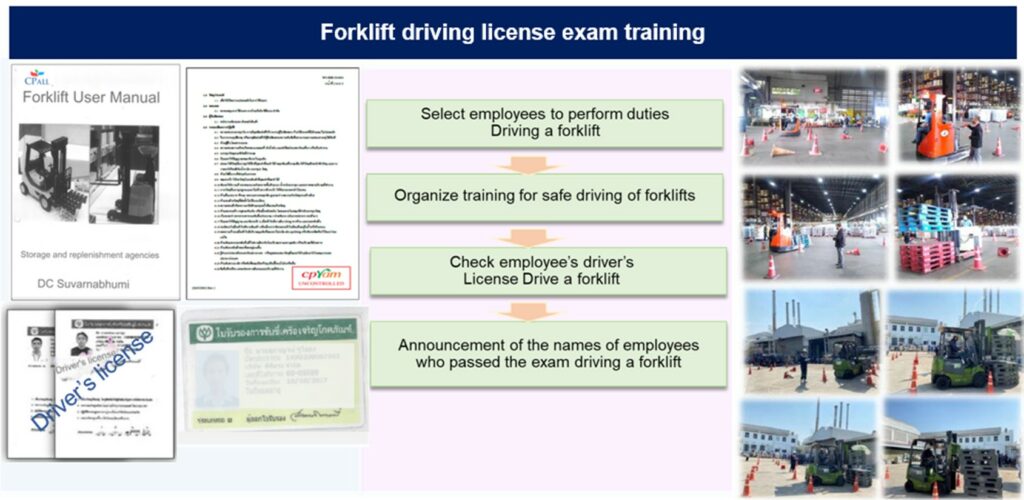
The program in construction contractor training on safety standards before working in 7-Eleven stores and distribution center areas and
CP RAM factory area
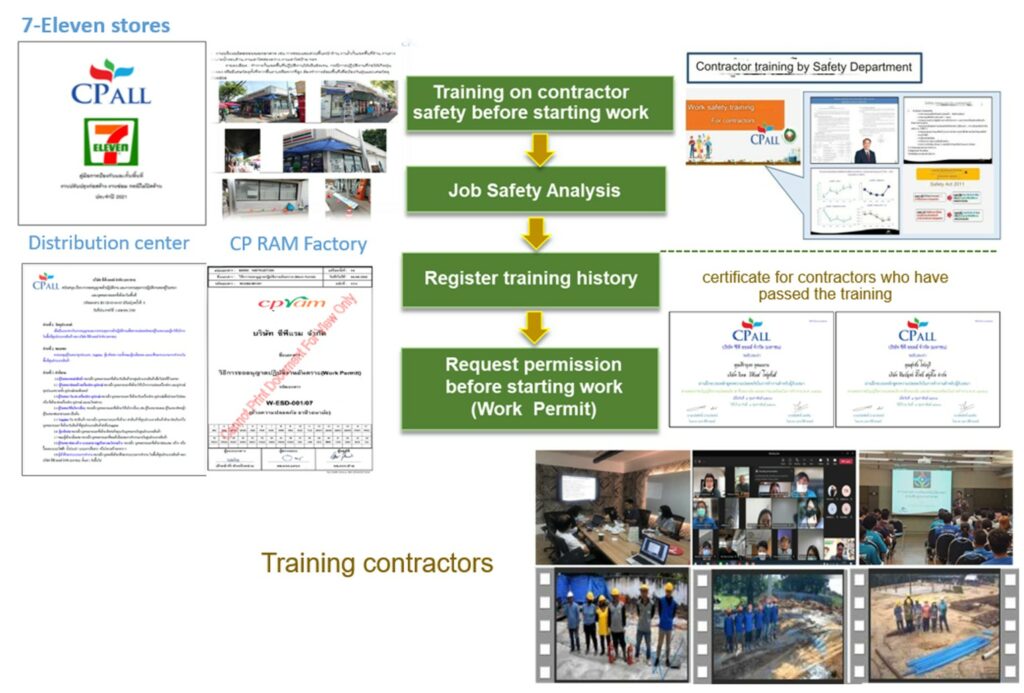
Transport Contractor Training Program: Professional Truck Driving Course
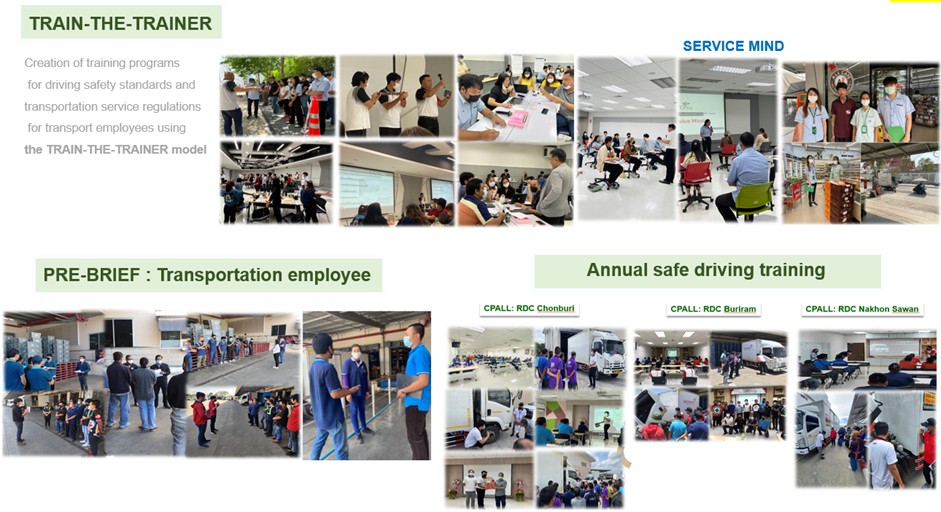
OHS criteria introduced in procurement and contractual requirements
The company focuses on procurement and hiring that may affect occupational health and safety. The Procurement Unit, that is involved with occupational health and safety, has established standards and guidelines for the procurement related to occupational health and safety for transport contractors, contractors, and external service providers. The tasks include preliminary qualifications of the safety-related contractor in a document that defines the scope and details of the mission the Company wants the contractor to perform, and other responsibilities related to the mission (Terms of Reference: TOR), as well as including the requirement of compliance with safety regulations and occupational health and work environment as one of the assessment/selection criteria for contractors, suppliers, and external service providers. This is to ensure that the procurement process is consistent with the law, risk aspects, the policies and measures to control risks related requirements, including occupational health and safety management system requirements.
Other Information
Performance Data of Occupational Safety, Health and Working Environment
GRI Standard | Required Data | Unit | 2019 | 2020 | 2021 | 2022 | ||||
Male | Female | Male | Female | Male | Female | Male | Female | |||
Employee | ||||||||||
403-9 (a) 2018 | – The number of fatalities as a result of work-related injury | Persons | 0 | 2 | 5 | 0 | ||||
0 | 0 | 2 | 0 | 2 | 3 | 0 | 0 | |||
– Fatalities rate | Cases/1,000,000work hours | 0 | 0.008 | 0.013 | 0 | |||||
0 | 0 | 0.02 | 0 | 0.013 | 0.013 | 0 | 0 | |||
– The number of high-consequence work-related injuries (excluding fatalities) | Persons | 0 | 1 | 3 | 2 | |||||
0 | 0 | 0 | 1 | 2 | 1 | 1 | 1 | |||
– High-consequence work-related injuries rate (excluding fatalities) | Cases/1,000,000work hours | 0 | 0.004 | 0.01 | 0.01 | |||||
0 | 0 | 0 | 0.01 | 0.01 | 0.004 | 0.01 | 0.004 | |||
– The number of recordable work-related injuries | Persons | 272 | 539 | 771 | 720 | |||||
170 | 102 | 252 | 287 | 351 | 420 | 366 | 354 | |||
– Recordable work-related injuries rate | Cases/1,000,000work hours | 1.22 | 2.14 | 2.00 | 1.93 | |||||
2.27 | 0.69 | 3.02 | 1.99 | 2.23 | 1.84 | 2.74 | 1.49 | |||
– Lost-Time Injuries Frequency Rate (LTIFR) | Cases/1,000,000work hours | 0.71 | 1.66 | 1.69 | 1.65 | |||||
1.28 | 0.43 | 2.21 | 1.38 | 1.80 | 1.62 | 2.22 | 1.29 | |||
– The number of hours worked | Hours | 222,630,585 | 251,718,321 | 386,155,115 | 372,331,111 | |||||
74,829,447 | 147,801,138 | 83,430,837 | 168,287,484 | 157,467,972 | 228,687,144 | 135,490,551 | 236,840,560 | |||
403-10 (a) 2018 | – The number of fatalities as a result of work-related ill health | Persons | 0 | 0 | 0 | 0 | ||||
0 | 0 | 0 | 0 | 0 | 0 | 0 | 0 | |||
– The number of cases of recordable work-related ill health | Cases | 0 | 0 | 1 | 0 | |||||
0 | 0 | 0 | 0 | 1 | 0 | 0 | 0 | |||
– Occupational Illness Frequency Rate (OIFR) | Cases/1,000,000work hours | 0 | 0 | 0.003 | 0 | |||||
0 | 0 | 0 | 0 | 0.01 | 0 | 0 | 0 | |||
Contractor | ||||||||||
403-9 (b) 2018 | – The number of fatalities as a result of work-related injury | Persons | 0 | 3 | 9 | 12 | ||||
0 | 0 | 2 | 1 | 8 | 1 | 7 | 5 | |||
– Fatalities rate | Cases/1,000,000work hours | 0 | 0.01 | 0.03 | 0.05 | |||||
0 | 0 | 0.02 | 0.01 | 0.05 | 0.01 | 0.07 | 0.03 | |||
– The number of high-consequence work-related injuries (excluding fatalities) | Persons | 0 | 0 | 2 | 1 | |||||
0 | 0 | 0 | 0 | 1 | 1 | 0 | 1 | |||
– High-consequence work-related injuries rate (excluding fatalities) | Cases/1,000,000work hours | 0 | 0 | 0.007 | 0.004 | |||||
0 | 0 | 0 | 0 | 0.01 | 0.01 | 0 | 0.01 | |||
– The number of recordable work-related injuries | Persons | 96 | 120 | 306 | 267 | |||||
68 | 28 | 71 | 49 | 186 | 120 | 153 | 114 | |||
– Recordable work-related injuries rate | Cases/1,000,000work hours | 1.51 | 0.52 | 1.00 | 1.01 | |||||
20.2 | 0.93 | .080 | 0.34 | 1.16 | 0.82 | 1.42 | 0.72 | |||
– Lost-Time Injuries Frequency Rate (LTIFR) | Cases/1,000,000work hours | 0.99 | 0.37 | 0.74 | 0.80 | |||||
1.28 | 0.67 | 0.52 | 0.28 | 0.73 | 0.75 | 1.10 | 0.59 | |||
– The number of hours worked | Hours | 63,698,344 | 232,938,058 | 306,063,307 | 264,671,376 | |||||
33,717,995 | 29,980,349 | 88,997,868 | 143,940,189 | 160,289,943 | 145,773,363 | 107,389,032 | 157,282,344 | |||
403-10 (b) 2018 | – The number of fatalities as a result of work-related ill health | Persons | 0 | 0 | 0 | 0 | ||||
0 | 0 | 0 | 0 | 0 | 0 | 0 | 0 | |||
– The number of cases of recordable work-related ill health | Cases | 0 | 0 | 1 | 0 | |||||
0 | 0 | 0 | 0 | 1 | 0 | 0 | 0 | |||
– Occupational Illness Frequency Rate (OIFR) | Cases/1,000,000work hours | 0 | 0 | 0 | 0 | |||||
0 | 0 | 0 | 0 | 0 | 0 | 0 | 0 |
Remark
1) Types of accident-related injuries cases of high-consequence work-related injuries of employees and contractor in 2022 include:
– Employees, 2 cases, disability type (loss of organs, limbs)
– Contractor, 1 case, type of disability (loss of organs, limbs)
2) In 2022, the scope of employee data reporting was expanded. Cover subsidiaries as follows:
– Ek-Chai Distribution Systern Co.,Ltd. Start reporting data from the year 2021 onwards
– CP ALL Plc. expanded its scope to cover Education area and CPRAM Co., Ltd. reports covering all areas
3) In 2022, the scope of contractor data reporting was expanded as follows:
– CP ALL Plc.report data of contractors hauling good within the distribution center
– Ek-Chai Distribution Systern Co.,Ltd. report data of construction contractor, facility Management contractor, security Officer, housekeeper, product introduction staff at the branch (PC), food shop staff for employees, shop staff for rent and transportation contractor
– CPRAM Co., Ltd. report data of contractor selling food in the factory, nurse and supplie
4) The formula for calculating safety data for the year 2022 is as follows:
– High-consequence work-related injuries rate (excluding fatalities) = Total number of work-related injury (cases) that results in an injury which the worker cannot expected to recover fully to pre-injury health status within 6 months over the reporting period X 1,000,000 hours worked / Number of hours worked (over the reporting period)
– Recordable work-related injuries rate = Total number of injuries (cases) at all levels including work-related injury from restricted work, beyond first-aid level, lost-day level to severity level over the reporting period X 1,000,000 hours worked / Number of hours worked (over the reporting period)
– Lost-Time Injuries Frequency Rate (LTIFR) = Total number of lost time injuries (cases) over the reporting period x 1,000,000 hours worked / Total hours worked (over the reporting period)
– Occupational illness Frequency Rate (OIFR) = Total number of occupational diseases (cases) over the reporting period x 1,000,000 hours worked / Total hours worked (over the reporting period)
Related policies and Guideline
Safety, Health and Working Environment Policy | Download |